Silicon carbide
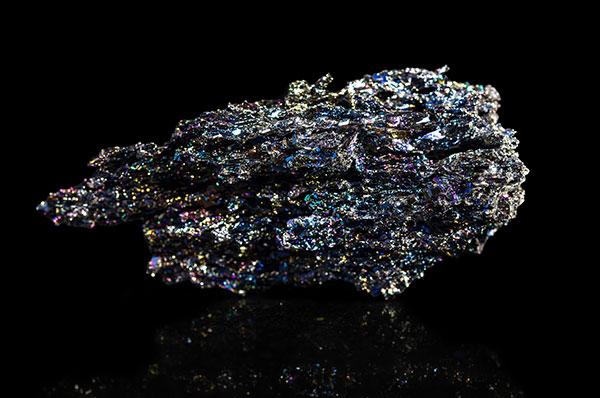
Silicon carbide is obtained from the reaction of silicon dioxide and carbon in a resistance furnace. In practice, it is a mixture of petroleum coke and quartz sand. The resulting product obtained from this mixture is silicon carbide, which is then sorted and crushed to the required grain size. Metallurgical silicon carbide has a silicon carbide content of 90% and is widely used in modern metallurgy.
Application:
Silicon carbide (SiC) is used for cast iron inoculation. SiC with a purity of approximately 85% is used to obtain cast iron with flake graphite, while SiC with a purity of 88-95% tends to be preferred for spheroidal graphite.
Advantages:
- More economical than FeSi (ferrosilicon)
- Demonstrated positive impact on cast iron in the form of decreased tendency to form cavities
- Increased share of scrap steel in charges
- Stabilisation of mechanical properties
We offer a broad range of quality SiC products. Simply send us your inquiry.
We also offer briquettes for use in cupola ovens.
Resorbent – SiC90
Parameters | Value [%] | ||
Silicon carbide | SiC | Min. 90,00 | Ø 91,3 |
Iron | Fe | Max. 0,50 | |
Carbon | Cfix | Max. 3,00 | |
Moisture | Wtr | Max. 0,50 | |
Grain size | 0-1 ; 0-10; 1-10; 0-20; 1-20 [mm] | ||
Packaging: | Bags: 20; 25 kg ; Big Bag po 1t; loose delivery |